◐ Equipment Features
1.The equipment is with accurate controlling process and high level mechanic designing, which is simple to operate and runs stably.
2.Equipped with water cooling rasp and automatic blades renew device. The blades can be used with 80% more working endu rance.
3.The buffing quality can be proved more stable in accordance ofthe working of automatic belt measuring device.
4.Casing drove by expandable rim, in order to ensure dynamic performance ofthe retread tires.
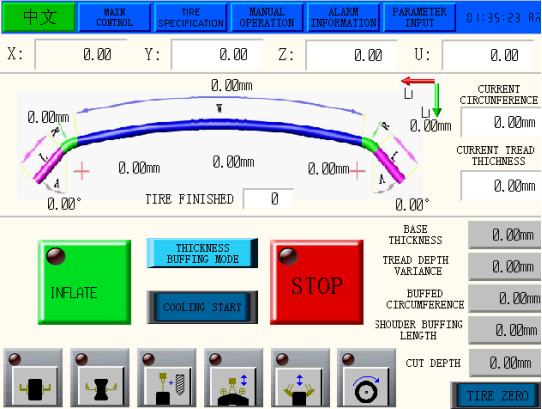
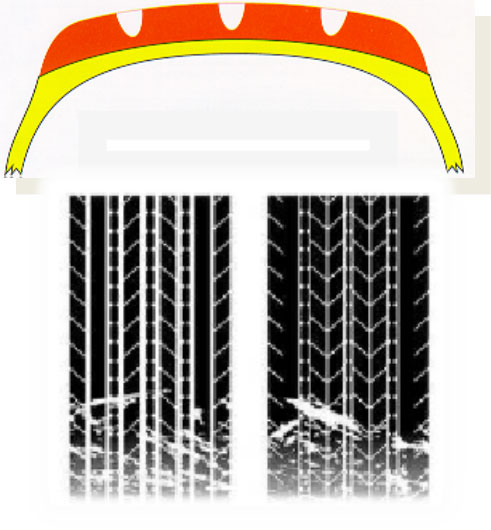
Buffing station requirements
◐ Suggested configuration/tools
1. Exhaust and dust removal system
2. Taper and needle-nosed pliers (cut the leaking wire)
3. Tire marking chalk (mark the location of the wound, tread width, etc.)
4. Lubricating agent of expansion wheel (apply regularly)
5. Tire parameter table (input PC configuration table in advance, and call it out directly when polishing)
6. Tread base measuring ruler/pattern depth meter/flexible tape measure (can be used for phased detection)
7. RMA standard grinding roughness template (used to judge the wear of grinding tool head)
8. Goggles with side protection
9.Safety shoes
◐ Process conditions
1.Compressed air pressure: 5 ~ 8kg/cm
2.Tire inflation pressure: 1.5kg /cm2.
◐ Buffing position quality standard
0 (emphasis). Install the tire on the sander and inflate it.
To properly install and fix the tire, it is recommended to do the following,
Make sure the expansion rim is properly lubricated
During the filling, turn the tire slowly
1.after grinding the tire, the grinding surface should be maintained with a 1.5~2.5mm rubber layer.
2.After grinding , tire body line area for one place may not be greater than 1% of the area of the tyre abrasion,;
Total out-line area shall not be greater than 2%, polishing line depth does not hurt cord fabric layer.
3. after grinding ,tire puncture holes and other defects of each tire shall not exceed 3, and the distance between the two wounds shall not be less than 1/6 of the tire circumference.
4. Grinding requirements:
4.1 grinding depth shall be controlled at 1.5-2mm.Rough finish of polished surface :RMA 3 ~ 5.
4.2 grinding surface deviation, tire crown grinding surface deviation is not greater than 1MM °
4.3 the width of the polished crown shall be equal to or less than 1/16 inch (2mm) of the base width of the tread, and the tread dimensions used shall be in accordance with the tire parameters (the grinding radius of the machine shall be set in accordance with the tire parameters).
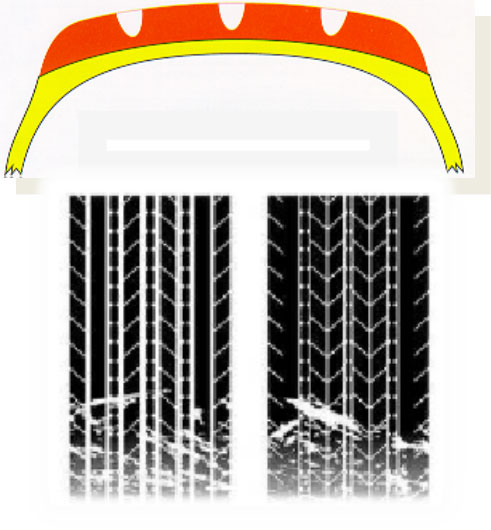
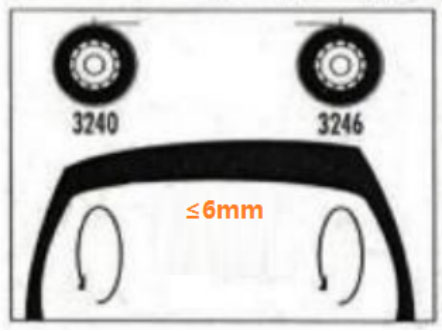
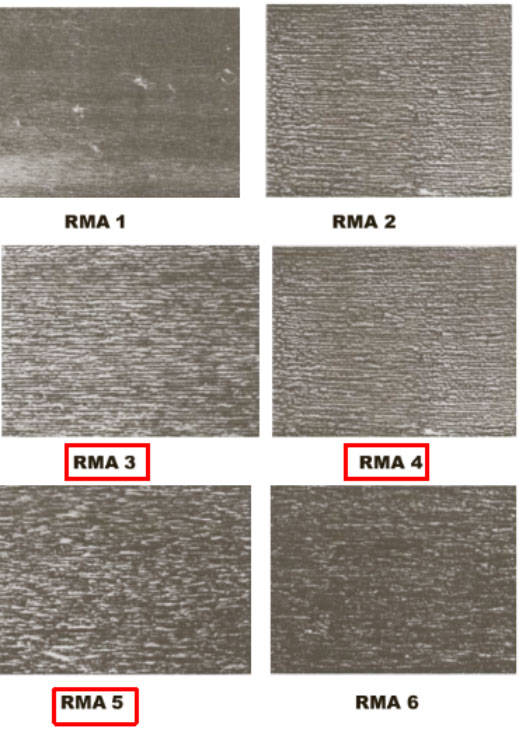
5. Fishing:
- polish to original tread width as much as possible
- when it is necessary to repair and grind the tire shoulder, turn the grinding head support to 30 ~ 40°, and trim the double shoulder Angle symmetrically, so that the distance between the center of the tire crown and the double rim is equal as far as possible.
-- DPC: make the trim width equal to that of the tread.
- no DPC:
Heavy duty retread: make retread width equal to retread tread width.
Light retouching tread: make the retouching width less than the retouching tread tread width (1.6mm less on each side)
TRAC ring retread: make the dressing width less than the width of retread tread (3.2mm less on each side)
- if the tyre shoulder Angle gap is close to 13mm, retread with gap rubber.
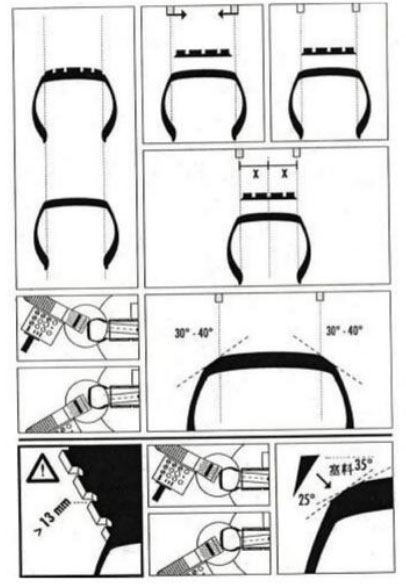
◐ Safet
1.Before buffing, eliminate the visible foreign matter, including stone, nails, screws, etc.
2.inflatable no more than 15 psi (1.5 Kg/cm2).
3. labor protection glasses
4. not allowed to wear gloves and wear comfortable clothes
5.long hair must be bandaged up
Please refer to the manual grinding machine equipment, understand any security problems.
◐ Production objectives
1. Safe production;
2. process standardization, efficiency maximization, production of fine Retreading tires.







